Disruptive Cable Technologies Revolutionizing Machine Vision Systems
As machine vision systems evolve to meet demands for higher speeds, precision, and connectivity, traditional copper cables are increasingly becoming a bottleneck. Enter disruptive cable technologies—innovative materials, designs, and integration strategies that redefine reliability, bandwidth, and adaptability. From self-healing materials to fiber-optic hybrids, these breakthroughs are transforming how vision systems handle data, endure harsh environments, and integrate with Industry 4.0 ecosystems.
1. Fiber-Optic Cables: Beyond Bandwidth Limits
Fiber optics are no longer limited to telecom—they’re now a game-changer for high-speed vision systems.
Key Innovations
Hybrid Fiber-Copper Cables:
Combine fiber strands for high-speed data (e.g., 100 Gbps for 8K cameras) with copper wires for power delivery (PoE++).
Eliminate separate power and data lines, simplifying cable management.
Plastic Optical Fiber (POF):
Flexible, lightweight, and immune to EMI, ideal for robotic arms in automotive assembly lines.
Active Optical Cables (AOCs):
Embed optical transceivers directly into connectors, enabling plug-and-play 100-meter links without signal degradation.
Case Study: A German automotive plant replaced GigE Vision copper cables with OM5 multimode fiber in hybrid cables, achieving zero latency in real-time defect detection for autonomous welding robots.
2. Self-Healing Cable Jackets
Inspired by biomimicry, self-repairing materials minimize downtime in high-wear environments.
How It Works
Microcapsule Technology:
Jackets embedded with microcapsules release healing agents (e.g., silicone polymers) when cracks form.
Thermoplastic Elastomers (TPEs):
Heat-activated TPEs reflow to seal abrasions caused by friction in drag chains.
Applications:
Food processing plants where cables endure daily washdowns.
Mining operations with abrasive dust and vibrations.
Example: Lapp’s Ölflex FD 855 POCAN features a self-healing PUR jacket, reducing maintenance costs by 40% in packaging machinery.
3. Wireless and Power-over-Everything (PoX)
Cutting the cord isn’t just for consumer tech—industrial wireless solutions are gaining traction.
Wireless Vision Systems
Li-Fi (Light Fidelity):
Uses LED light to transmit data at 224 Gbps, immune to RF interference in EMI-heavy environments like welding shops.
5G Private Networks:
Ultra-low-latency wireless links for mobile vision systems on AGVs or drones.
Power-over-Everything (PoX)
Power over Fiber (PoF):
Transmit optical power alongside data, eliminating copper entirely for explosive environments (ATEX zones).
Multi-Protocol PoE:
IEEE 802.3bt delivers 90W over Ethernet, powering heated cameras in cold storage facilities.
Case Study: A pharmaceutical lab deployed Li-Fi-enabled cameras in sterile cleanrooms, avoiding RF emissions that disrupt sensitive instruments.
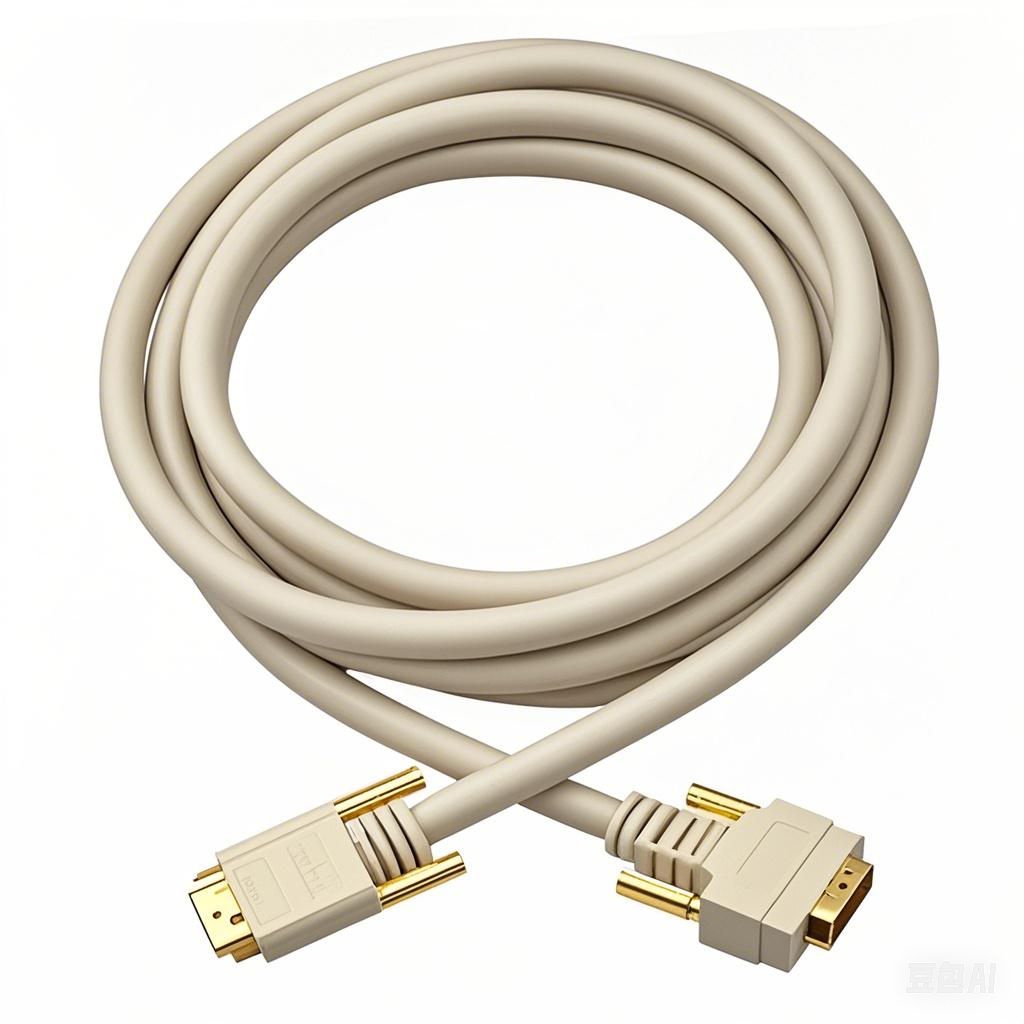
4. Shape-Memory and Modular Cables
Adaptive cables that “learn” their environment and simplify reconfiguration.
Shape-Memory Polymers (SMPs)
Cables return to their original shape after bending, reducing stress in robotic applications.
Example: Fujikura’s SMP-jacketed cables for articulated inspection robots in semiconductor fabs.
Modular Magnetic Connectors
Magnetic M12 Connectors:
Snap-fit design allows tool-free reconfiguration of camera arrays.
Automatically disconnect under excess tension, preventing damage.
USB4 Modular Cables:
Hot-swappable adapters switch between USB, HDMI, or Ethernet protocols.
Use Case: A solar panel inspection drone uses magnetic connectors to swap cameras based on thermal or visual inspection needs.
5. Graphene and Nanomaterial-Enhanced Cables
Nanomaterials are unlocking unprecedented conductivity and durability.
Graphene-Coated Conductors
Benefits:
20% lower resistance than pure copper.
Corrosion-resistant, even in saltwater environments (e.g., offshore rigs).
Application:
High-speed coastal surveillance cameras with graphene-infused coaxial cables.
Carbon Nanotube Shielding
Replaces traditional braided shields, offering 360° EMI protection at 1/3 the weight.
Used in aerospace vision systems to reduce cable mass by 50%.
Example: TE Connectivity’s Nanonics cables use carbon nanotube films to block 90 dB of EMI in MRI-guided surgical robots.
6. Smart Cables with Embedded Sensors
Cables that double as diagnostic tools for predictive maintenance.
Key Features
Strain and Temperature Sensors:
Detect micro-cracks or overheating in real time via IoT platforms.
Voltage Monitoring:
Alert technicians to insulation breakdown or power surges.
GPS Tracking:
Locate cables in sprawling facilities like shipyards or warehouses.
Integration:
Siemens’ MindSphere-enabled cables send health data to AI-driven maintenance systems, predicting failures 3 weeks in advance.
7. Eco-Conscious Cable Designs
Sustainability meets performance in next-gen vision systems.
Biodegradable Jackets
Made from plant-based polymers (e.g., corn starch) that decompose in 2 years.
Deployed in eco-sensitive industries like agriculture.
Recyclable Aluminum Conductors
Replace copper with conductive aluminum alloys, reducing carbon footprint by 60%.
Example: Igus’ Chainflex CFSPECIAL.192 cables for solar farm inspection robots.
Challenges and Future Outlook
While disruptive, these technologies face hurdles:
Cost: Graphene and fiber optics remain expensive for small-scale operations.
Standardization: Fragmented protocols (e.g., USB4 vs. Optical Thunderbolt) complicate adoption.
Skills Gap: Technicians need training to handle advanced materials and diagnostics.
Future Trends:
Quantum Communication Cables: Tamper-proof data links for secure vision systems.
3D-Printed Cables: On-demand customization for unique industrial setups.