How Cables Enable Vision Systems in Space”
1. Introduction
Space exploration demands vision systems that function in conditions far beyond terrestrial limits. Whether guiding a rover across Martian terrain or aligning a telescope to observe distant galaxies, these systems depend on cables capable of transmitting high-fidelity data while enduring cosmic radiation, temperature swings of 300°C, and zero-gravity mechanical fatigue. The design and materials of these cables determine whether humanity’s eyes in space remain open—or go blind.
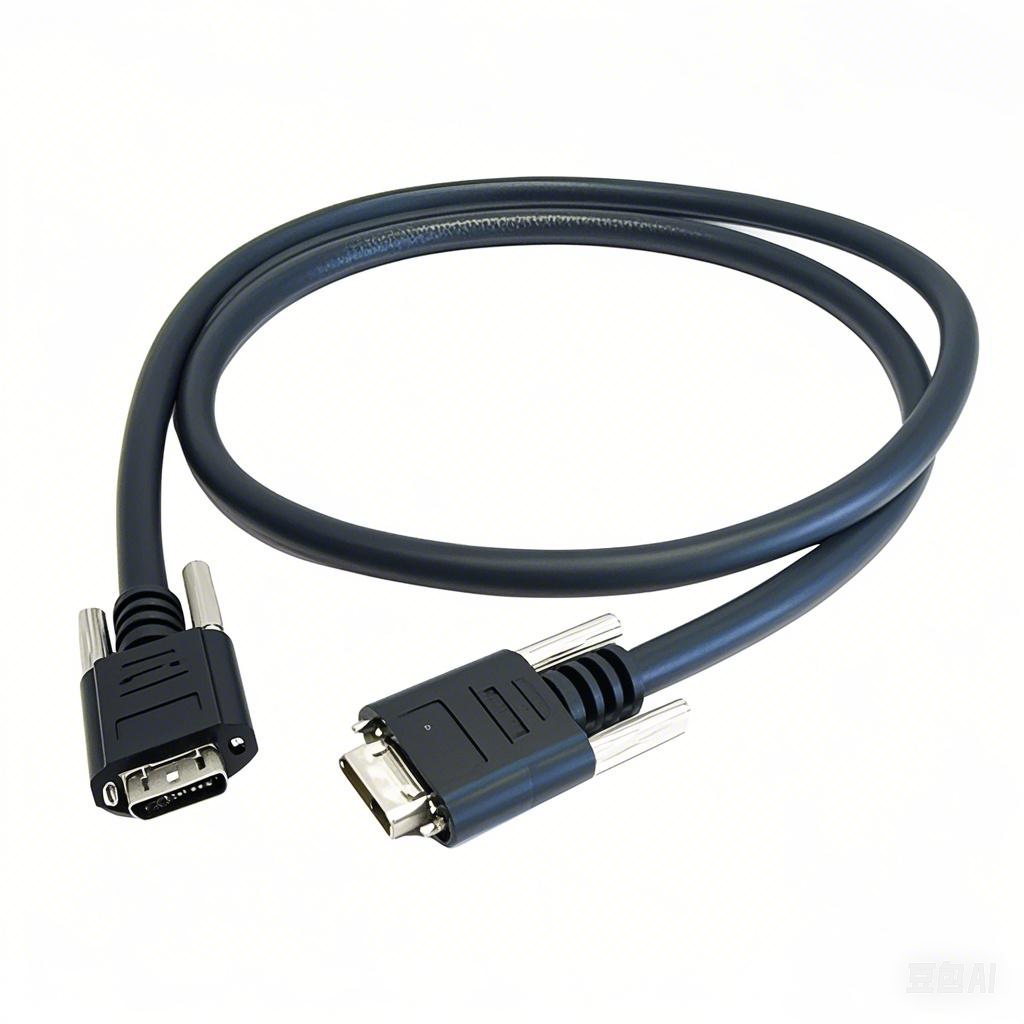
2. Space Environment: Challenges for Cables
2.1 Thermal Extremes
Lunar Surfaces: Temperatures ranging from -173°C (night) to +127°C (day).
Sunlit vs. Shadowed Zones: Cables crossing spacecraft joints face rapid thermal cycling.
2.2 Radiation Exposure
Solar Particle Events (SPEs): High-energy protons degrading insulation materials.
Galactic Cosmic Rays (GCRs): Cumulative ionizing radiation causing signal degradation.
2.3 Vacuum and Outgassing
Material Degradation: Polymers releasing volatile compounds that condense on optical sensors.
Cold Welding: Metal connectors fusing in vacuum without proper coatings.
2.4 Mechanical Stress
Launch Vibrations: 20 G-force shocks during rocket ascents.
Microgravity Fatigue: Cables in robotic arms bending 10,000+ times during deployment.
3. Space-Grade Cable Design Principles
3.1 Materials Science
Insulation:
Polyimide (Kapton®): Withstands -269°C to +400°C, low outgassing (NASA-approved).
PTFE (Teflon®): Radiation-resistant, minimal dielectric loss for high-speed signals.
Shielding:
Multi-Layer Foil + Braid: Blocks EMI from spacecraft electronics and solar flares.
Gold-Plated Conductors: Prevents oxidation in oxygen-free environments.
3.2 Connector Innovations
MIL-DTL-38999 Series: Hermetically sealed, triple-start threaded connectors for vacuum integrity.
Magnetic Latching: Zero-gravity-compatible connectors for robotic arm camera systems.
3.3 Signal Integrity
Impedance Control: 50Ω/75Ω matched cables for GHz-range data transmission.
Rad-Hard Fibers: Fluorine-doped optical fibers resisting darkening from gamma rays.
4. Vision Systems Enabled by Space Cables
4.1 Planetary Rovers
Perseverance Rover (Mars 2020):
Cable Tech: Shielded twisted-pair cables transmitting 20 MPixel images via 2 Mbps deep-space RF links.
Challenge: Surviving 96 sols (Martian days) of dust storms and -100°C nights.
Outcome: 200+ gigabytes of surface data relayed to Earth.
4.2 Earth Observation Satellites
Landsat-9 Multispectral Imager:
Cables: Ultra-flexible coaxial bundles routing 12-bit data from SWIR sensors.
Bandwidth: 3.5 Gbps downlink via X-band RF cables to ground stations.
4.3 Deep-Space Telescopes
James Webb Space Telescope (JWST):
Cryogenic Cables: Niobium-tin superconducting wires operating at 4K for NIRCam detectors.
Data Flow: 57 Gbps routed through 10-layer flex PCBs to onboard solid-state recorders.
5. Failure Modes and Mitigation
Single-Event Upsets (SEUs): Radiation-induced data corruption mitigated by error-correcting codes (ECC) in LVDS cables.
Abrasion in Dusty Environments: Rover cable jackets reinforced with atomic-oxygen-resistant coatings.
Thermal Expansion Mismatch: Carbon-fiber-reinforced cables aligning CTE with titanium camera housings.
6. Standards and Testing
NASA-STD-6016: Requirements for electrical wiring for space applications.
ESA ECSS-Q-ST-70-02C: Outgassing tests for materials in vacuum.
MIL-STD-1540: Vibration and shock testing for launch survivability.
7. Future Trends
7.1 Autonomous Repair
Self-Healing Polymers: Cables regenerating insulation cracks caused by micrometeoroid impacts.
Robot-Assisted Splicing: ISS-based robots replacing damaged cable segments during EVAs.
7.2 Quantum Communication
Entangled Photon Links: Space-to-ground quantum key distribution (QKD) via ultra-low-loss fibers.
7.3 Sustainable Materials
Bio-Based Polyimides: Reducing reliance on petrochemical-derived insulation.
In-Situ Resource Utilization (ISRU): Manufacturing cables on Mars using regolith-derived silica.