How to Choose Moisture-Resistant Cable Materials
In environments where humidity, water exposure, or condensation are constant threats, selecting the right cable materials is critical to ensuring long-term reliability and performance. From offshore wind farms to food processing plants, moisture can degrade insulation, corrode conductors, and lead to catastrophic failures.
1. The Risks of Moisture in Cable Systems
Moisture ingress can cause:
Insulation Breakdown: Water treeing in polymers, leading to short circuits.
Conductor Corrosion: Oxidation of copper or aluminum, increasing resistance and heat generation.
Mold Growth: Organic growth in humid environments, degrading jacket integrity.
Electrical Leakage: Reduced dielectric strength, risking shocks or fires.
Example: A wastewater treatment plant reported a 40% failure rate in control cables within 2 years due to hydrolysis of PVC jackets in humid, acidic air.
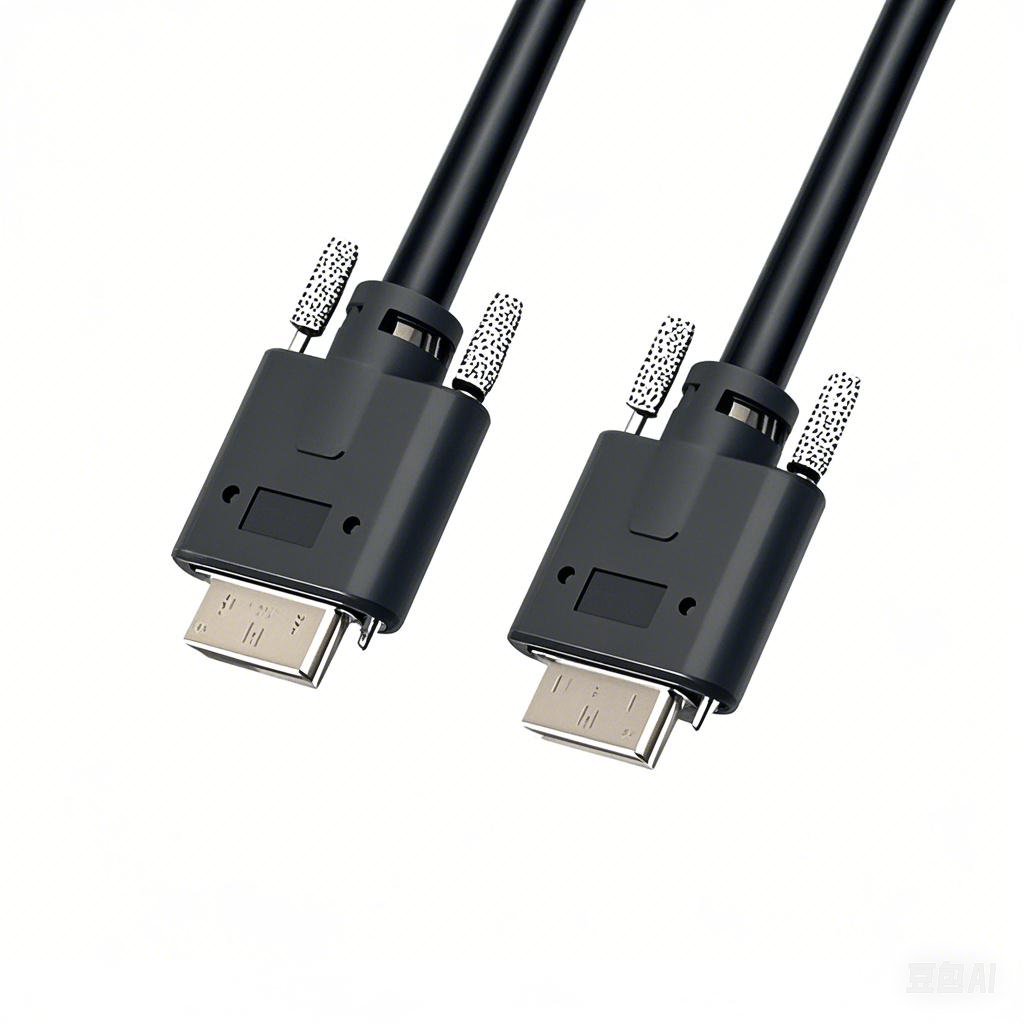
2. Key Material Properties for Moisture Resistance
A. Water Blocking
Hydrophobic Materials: Silicone or fluoropolymers (e.g., FEP, PTFE) repel water molecules.
Tape Barriers: Aluminum-polyester laminated tapes prevent longitudinal water migration.
Gel-Filled Cores: Flood cables use hydrophobic gels to block moisture ingress.
B. Corrosion Resistance
Tinned Copper Conductors: Tin coating protects against oxidation in saltwater or acidic environments.
Stainless Steel Braiding: Armored cables for marine applications.
C. Chemical Resistance
Oil-Resistant Jackets: Materials like Chlorinated Polyethylene (CPE) withstand oils and solvents.
Acid/Base Resistance: ETFE or PVDF jackets for pH extremes.
D. Flexibility in Wet Conditions
Thermoplastic Elastomers (TPE): Maintain flexibility at -40°C to 90°C, even when wet.
Cold-Flex PVC: Prevents cracking in freezing, damp environments.
3. Top Moisture-Resistant Cable Materials
Material Strengths Limitations Best Applications
Silicone -50°C to 200°C, UV/ozone resistant Poor abrasion resistance High-temp steam environments
Polyurethane (PUR) Abrasion-resistant, IP68 rated Degrades in alkaline oils Robotics, marine equipment
FEP (Fluorinated Ethylene Propylene) Low water absorption (<0.1%), chemical inert High cost Semiconductor fabs, labs
TPE (Thermoplastic Elastomer) Flexible, IP69K washdown rated Limited high-temp use Food & beverage processing
LSZH (Low Smoke Zero Halogen) Water-resistant, fire-safe Stiffens in cold temps Subways, tunnels
4. Critical Testing Standards for Moisture Resistance
IEC 60529 (IP Ratings):
IP67: Temporary immersion (1m depth for 30 mins).
IP68: Continuous submersion (manufacturer-specified depth/time).
UL 44/UL 83: Water immersion tests for insulation/jackets.
ASTM D570: Measures water absorption (%) after 24-hour submersion.
IEC 60811-1-3: Tests for insulation and sheath integrity in humid conditions.
Case Study:
Offshore wind farm cables require DNVGL-RP-0418 certification, which mandates 3,000-hour salt spray tests and 100% water-blocking validation.
5. Design Tips for Moisture-Prone Environments
A. Connector and Termination Protection
Overmolded Connectors: Prevent water ingress at cable ends (e.g., M12/M8 IP69K).
Heat-Shrink Tubing: Seal splices with adhesive-lined tubing.
B. Layered Construction
Triple Extrusion: Combines conductor stranding, moisture-blocking tape, and a PUR outer jacket.
Drain Wires: Channel condensation away from critical components.
C. Environmental Adaptations
Submersible Cables: Use buoyant fillers (e.g., aramid yarn) for underwater applications.
UV-Resistant Additives: Protect against solar degradation in humid outdoor settings.
6. Industry-Specific Solutions
Marine & Offshore
NMEA 0400-compliant cables with tinned copper and neoprene jackets.
Example: Belden MarineTuff resists saltwater corrosion at depths up to 500m.
Food Processing
FDA-compliant PUR cables with smooth surfaces to repel grease and water.
Example: Lapp Ölflex FD 855 withstands daily high-pressure washdowns.
Renewable Energy
Solar Cable (TUV 2 PfG 1990): UV- and moisture-resistant for rooftop PV systems.
Hydroelectric Plant Cables: Gel-filled, stainless-armored designs for dam penstocks.
7. Cost vs. Performance Tradeoffs
Budget Option: PVC (limited to intermittent moisture; lifespan ~5 years).
Mid-Range: PUR (IP68, 10+ years in moderate humidity).
Premium: FEP/PTFE (near-zero water absorption, 20+ years in harsh conditions).
ROI Example:
A chemical plant switched from PVC to FEP-jacketed cables, reducing replacements from annual to once every 15 years—saving $120,000 in 10 years.
8. Future Trends
Self-Healing Polymers: Automatically seal minor cracks caused by moisture cycles.
Graphene Coatings: Ultra-thin, impermeable layers for lightweight moisture resistance.
Smart Moisture Sensors: Cables with embedded humidity detectors alerting via IoT.