Machine Vision Cables with Built-in Signal Amplifiers
In the fast-paced world of industrial automation, machine vision systems demand flawless data transfer to ensure precision in tasks like defect detection, robotic guidance, and real-time analytics. However, traditional cables often struggle with signal degradation over long distances or in noisy environments. Enter machine vision cables with built-in signal amplifiers—a game-changing innovation that boosts performance, extends range, and simplifies complex setups.
The Challenge of Signal Degradation in Machine Vision
Machine vision systems rely on high-bandwidth interfaces like CoaXPress, GigE Vision, and USB3 Vision to transmit image data at speeds exceeding 10 Gbps. However, as cable length increases:
Signal attenuation reduces image clarity.
Electromagnetic interference (EMI) from motors or power lines introduces noise.
Latency disrupts synchronization in multi-camera setups.
Traditional solutions, such as external repeaters or fiber optic converters, add cost, complexity, and points of failure. Integrated signal amplifiers embedded within cables address these issues at the source.
How Built-in Signal Amplifiers Work
These cables incorporate miniature amplification circuits directly into their connectors or along the cable jacket. Key technologies include:
Active Copper Cables (ACC):
Embed low-power amplifiers to regenerate signals without converting to optical.
Support protocols like USB3 Vision up to 15 meters (beyond the standard 5-meter limit).
Coaxial Signal Boosters:
Amplify high-frequency signals in CoaXPress cables, enabling 100+ meter runs at 6.25 Gbps.
Embedded Power over Cable (PoC):
Deliver power and amplified data through a single cable, reducing clutter.
Key Advantages of Amplifier-Equipped Cables
1. Extended Transmission Distances
Example: CoaXPress cables with amplifiers achieve 150 meters at full bandwidth vs. 40 meters for passive cables.
Impact: Ideal for sprawling facilities like automotive assembly plants or solar farms.
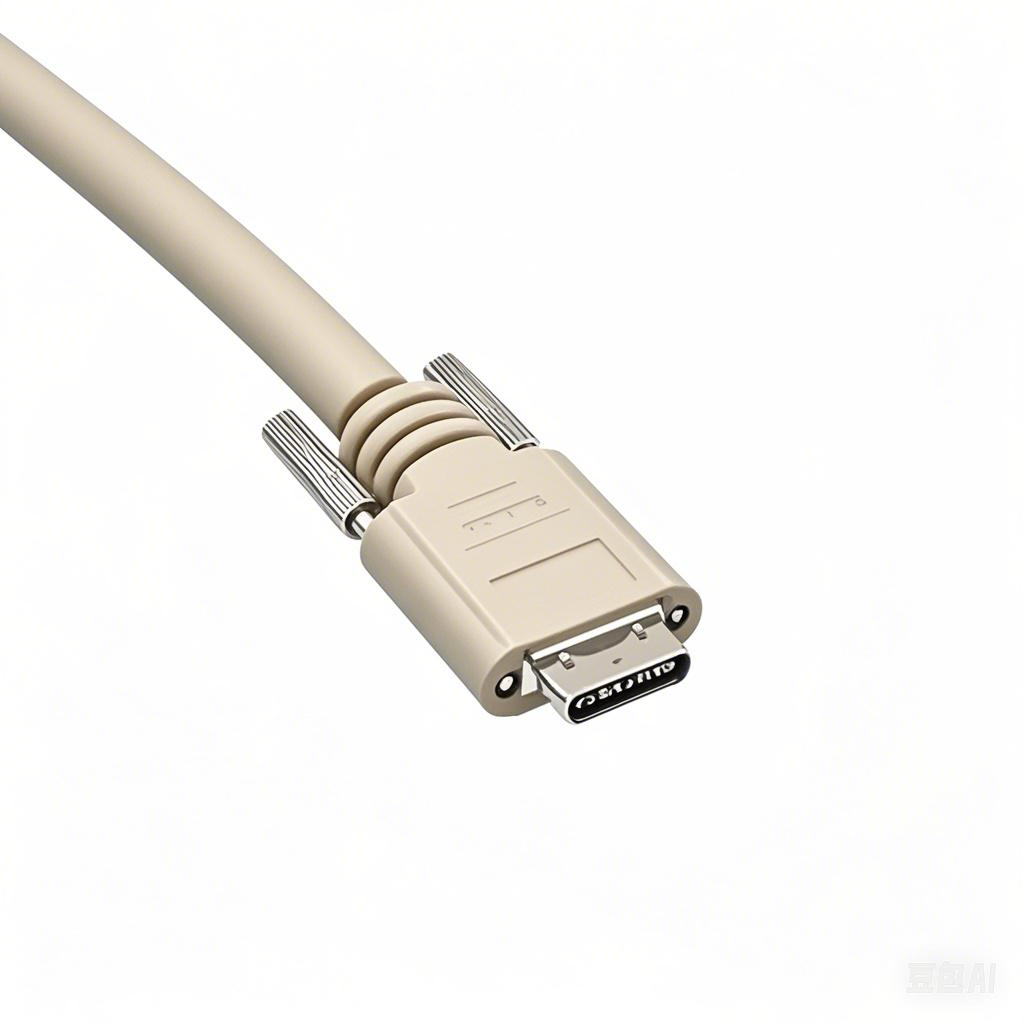
2. Enhanced Signal Integrity
Amplifiers counteract attenuation, preserving image resolution and reducing pixel errors.
Critical for high-speed inspections (e.g., semiconductor wafer scanning).
3. Reduced EMI Susceptibility
Onboard amplification strengthens signals, making them less vulnerable to noise from industrial machinery.
4. Simplified Infrastructure
Eliminate external repeaters, reducing cable management complexity and cost.
Use Case: AGV (Automated Guided Vehicle) systems with moving cameras benefit from fewer connection points.
5. Future-Proofing
Support higher data rates for next-gen vision systems (e.g., 8K cameras or 3D imaging).
Applications Transforming Industries
1. Automotive Manufacturing
Challenge: Cameras monitoring weld quality require long cable runs across factory floors.
Solution: Amplified GigE Vision cables maintain 10 Gbps throughput over 100 meters, ensuring real-time defect detection.
2. Pharmaceutical Packaging
Challenge: High-speed inspection of blister packs in sterile environments demands noise-free signals.
Solution: Shielded USB3 Vision cables with amplifiers resist EMI from conveyor motors while extending to 10 meters.
3. Agricultural Automation
Challenge: Drones and robotic harvesters need lightweight, long-range vision cables.
Solution: Thin, amplified coaxial cables enable 50-meter transmission for crop monitoring without signal loss.
4. Smart Warehousing
Challenge: Mobile robots with vision-guided navigation require reliable data links in dynamic layouts.
Solution: PoC-enabled cables deliver power and amplified data, avoiding frequent battery swaps.
Choosing the Right Amplified Cable
Match the Interface Standard
Ensure compatibility with your camera’s protocol (e.g., CoaXPress 2.0, GigE Vision).
Prioritize Shielding
Opt for double-shielded (foil + braid) designs in high-EMI environments.
Verify Power Requirements
Active cables may require external power; PoC options simplify integration.
Check Flexibility and Durability
For robotic arms or moving gantries, choose cables with high flex-cycle ratings.
Market Trends and Innovations
Miniaturization: Amplifier circuits are shrinking, enabling integration into ultra-thin cables.
AI-Driven Amplification: Smart cables with adaptive gain control optimize signals dynamically.
Hybrid Fiber-Copper Designs: Combine copper’s cost efficiency with fiber’s long-range capabilities.
Limitations to Consider
Cost: Amplified cables cost 20–50% more than passive ones but offset expenses by reducing auxiliary hardware.
Heat Management: Active components may generate heat; verify operating temperature ranges.