The Pros and Cons of Flexible vs. Rigid Cable Designs
When selecting cables for industrial, commercial, or residential applications, one critical decision engineers and designers face is choosing between flexible and rigid cable designs. Each type offers distinct advantages and limitations depending on the environment, installation requirements, and operational demands.
Understanding Flexible Cables
Flexible cables are engineered to bend and twist repeatedly without sustaining damage. They are constructed with stranded conductors and materials like thermoplastic elastomers (TPE) or PVC that prioritize pliability.
Pros of Flexible Cables
Dynamic Movement Compatibility
Ideal for applications requiring constant motion, such as robotics, automated machinery, or moving parts in elevators and cranes. Their ability to withstand bending cycles reduces wear and tear.
Ease of Installation
Flexibility simplifies routing through tight spaces, conduits, or complex machinery layouts. This reduces installation time and labor costs.
Vibration Resistance
Flexible designs absorb vibrations in environments like automotive systems or industrial pumps, minimizing the risk of conductor fatigue.
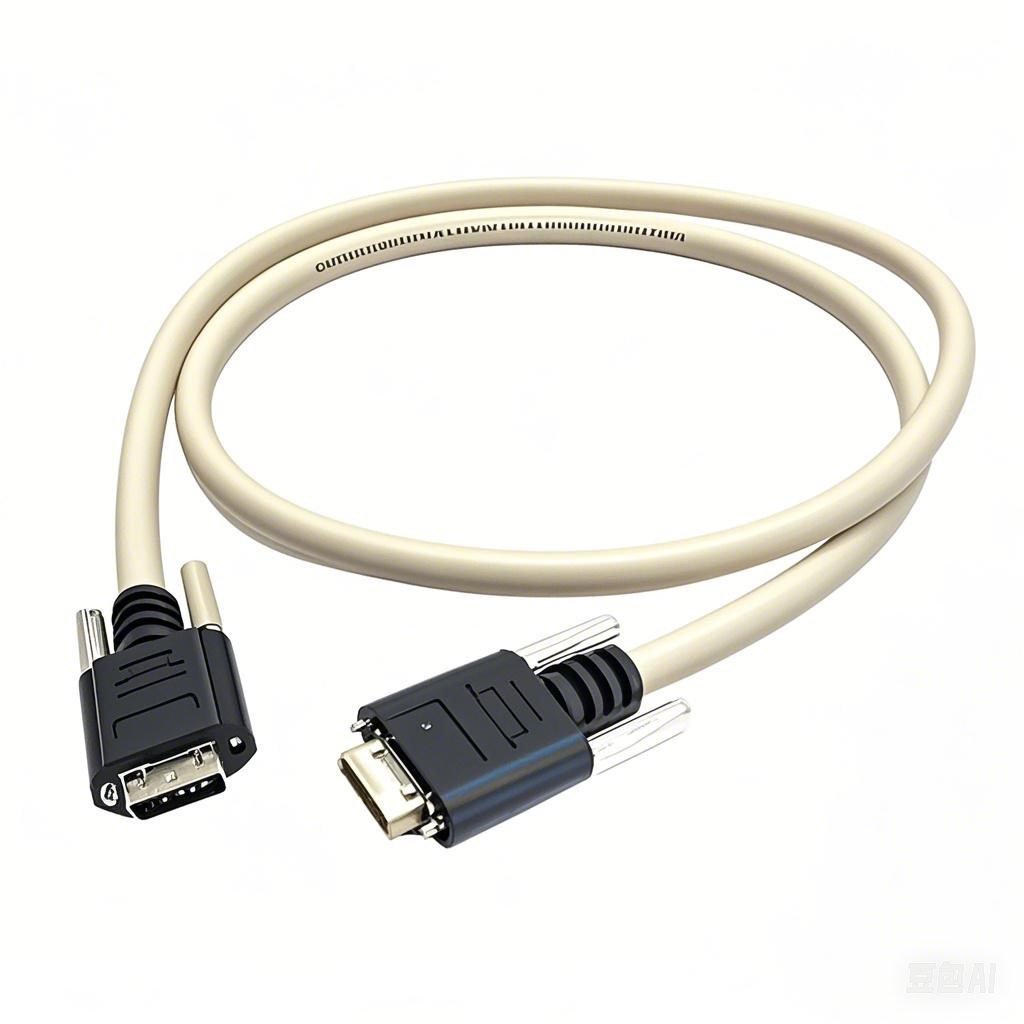
Lightweight
Stranded conductors and thinner insulation make flexible cables lighter, which is advantageous in aerospace or portable devices.
Cons of Flexible Cables
Higher Cost
Manufacturing stranded conductors and advanced polymers increases material and production costs compared to rigid designs.
Reduced Durability in Static Setups
If installed in fixed positions, flexible cables may sag over time, leading to potential stress points.
Lower Current Capacity
Stranded conductors have higher resistance than solid ones, limiting their use in high-power applications.
Understanding Rigid Cables
Rigid cables, also known as solid-core cables, use a single solid conductor and stiff insulation materials like cross-linked polyethylene (XLPE) or metal conduit. They are designed for stability and long-term reliability in static installations.
Pros of Rigid Cables
High Current Capacity
Solid conductors offer lower electrical resistance, making rigid cables suitable for high-power transmission in electrical grids, HVAC systems, and industrial machinery.
Cost-Effective
Simpler construction with solid conductors and basic insulation materials reduces manufacturing costs.
Durability in Fixed Installations
Rigid cables maintain shape and structural integrity over decades, ideal for underground wiring, building infrastructure, or outdoor power lines.
Better EMI Shielding
Stiffer designs often include robust shielding (e.g., armored jackets), protecting against electromagnetic interference in data centers or medical equipment.
Cons of Rigid Cables
Limited Flexibility
Bending or twisting rigid cables can cause permanent damage to conductors or insulation, leading to failure.
Complex Installation
Heavyweight and stiffness make them harder to route through tight spaces, often requiring specialized tools or additional labor.
Vulnerability to Vibration
In high-vibration environments (e.g., factories or vehicles), rigid cables are prone to cracking or connection loosening.
Flexible vs. Rigid Cables: Key Comparison
Factor Flexible Cables Rigid Cables
Bending Ability Excellent Poor
Current Capacity Moderate High
Installation Ease Easy Challenging
Cost Higher Lower
Durability in Motion Long-lasting Prone to damage
Best For Robotics, EVs, moving parts Fixed wiring, power grids
How to Choose the Right Design
Assess Movement Requirements
Choose flexible cables for dynamic applications (e.g., robotic arms).
Opt for rigid cables in static setups (e.g., building wiring).
Evaluate Environmental Stressors
Vibrations, temperature swings, or chemical exposure may favor flexible designs.
Harsh physical conditions (e.g., underground burial) often suit rigid cables.
Consider Long-Term Costs
While rigid cables are cheaper upfront, flexible cables may offer savings in maintenance and replacement for high-motion systems.
Review Industry Standards
Ensure compliance with certifications like UL, IEC, or MIL-SPEC, which often specify cable types for safety and performance.
Industry Applications
Flexible Cables:
Automotive wiring harnesses in electric vehicles.
CNC machines and 3D printers.
Medical devices requiring sterilization and movement.
Rigid Cables:
Residential and commercial electrical wiring.
Solar farm connections and wind turbine grounding.
Data center backbone cabling.