The Role of Connectors in Enhancing Machine Vision Cable Performance
1. Introduction
Machine vision systems demand precision, speed, and reliability to perform tasks such as real-time inspection, robotic guidance, and 3D scanning. As these systems evolve toward higher resolutions (e.g., 4K/8K cameras) and faster frame rates, the performance of interconnecting components becomes paramount. Connectors, which interface cables with devices, are pivotal in preserving signal quality, resisting environmental stressors, and minimizing downtime. A poorly designed connector can negate the benefits of even the most robust cable, leading to data corruption, latency, or system failures.
2. Connectors as Guardians of Signal Integrity
Signal integrity is the cornerstone of machine vision performance. Connectors influence this through:
2.1 Impedance Matching
High-speed protocols like CoaXPress-over-Fiber or 10GigE Vision require precise impedance control (typically 50Ω or 75Ω) to prevent reflections and signal loss. Connectors with impedance-matched contacts and dielectric materials ensure minimal discontinuity at cable-device junctions.
2.2 Contact Resistance and Material Science
Gold-Plated Contacts: Provide low contact resistance and corrosion resistance, ideal for low-voltage signals in high-humidity environments.
High-Density Configurations: Miniaturized connectors (e.g., Micro-BNC or M8/M12 circular connectors) support multi-channel data transmission without crosstalk.
2.3 Shielding Continuity
EMI shielding in cables must extend seamlessly through connectors. Metal-shell connectors with 360-degree grounding (e.g., shielded D-sub or M12 connectors) maintain a Faraday cage effect, blocking external interference.
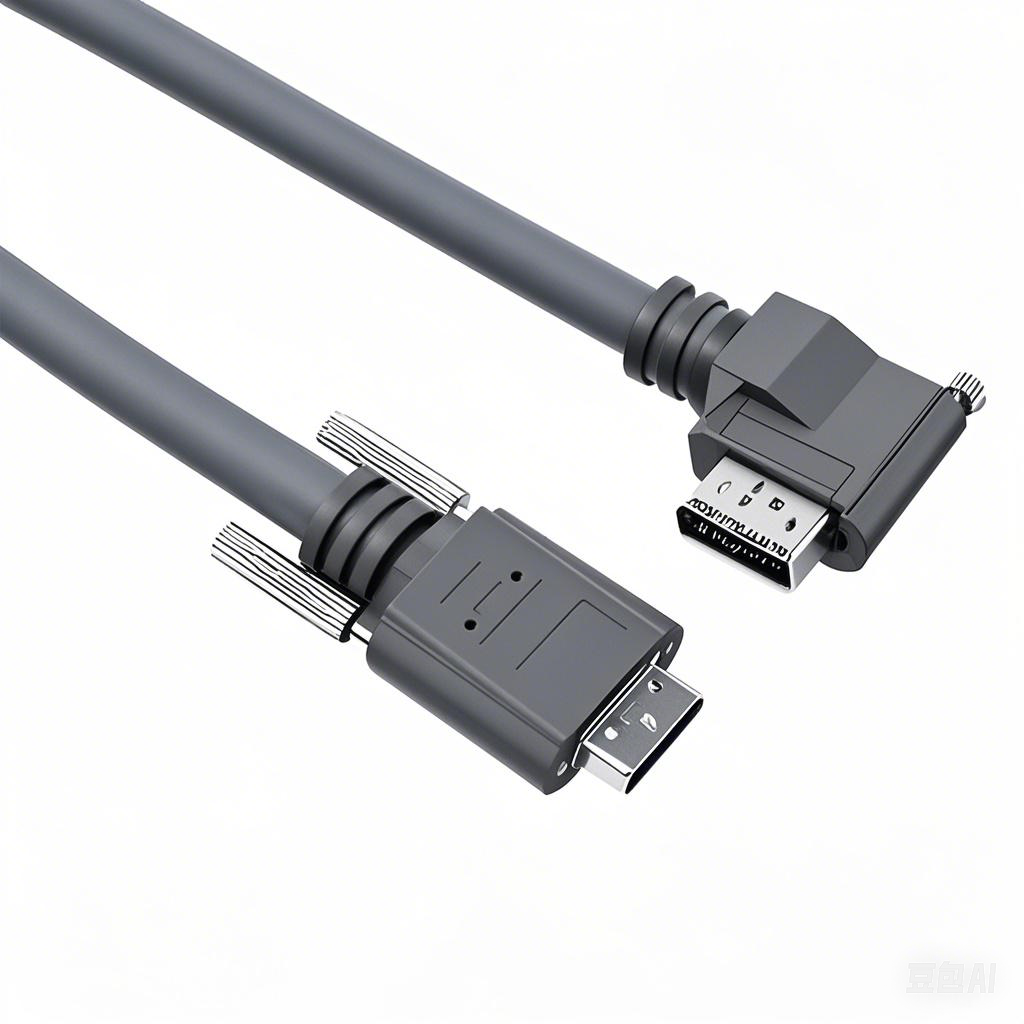
3. Connector Design for Harsh Environments
Industrial environments pose unique challenges that connectors must address:
3.1 Mechanical Durability
Vibration Resistance: Spring-loaded contacts or bayonet-style locking mechanisms (e.g., BNC connectors) prevent disconnection in high-vibration settings like automotive assembly lines.
IP Ratings: IP67/IP69K-rated connectors protect against dust, water jets, and chemical exposure, critical for food processing or outdoor applications.
3.2 Temperature Resilience
High-Temperature Plastics: Connector housings made of PEEK or PTFE withstand temperatures up to 200°C in foundries or semiconductor fabs.
Thermal Cycling Resistance: Materials with low coefficient of thermal expansion (CTE) prevent contact loosening in environments with rapid temperature shifts.
3.3 Chemical and Abrasion Resistance
Stainless Steel Shells: Resist corrosion in marine or chemical industries.
Overmolded Strain Relief: Reduces stress on cable-connector junctions in robotic arms or automated guided vehicles (AGVs).
4. Connector Innovations Enabling Next-Gen Vision Systems
Emerging technologies are pushing connector capabilities further:
4.1 Hybrid Connectors
Combine power, data, and coaxial signals in a single connector (e.g., hybrid M12), simplifying wiring in space-constrained systems like drones or surgical robots.
4.2 Fiber Optic Integration
Connectors with fiber optic termini (e.g., LC or SC connectors) support ultra-high-speed data transfer for hyperspectral imaging or LiDAR systems.
4.3 Smart Connectors
Embedded sensors monitor parameters like temperature, mating cycles, or EMI levels, enabling predictive maintenance and real-time diagnostics.
4.4 Modular and Field-Terminable Designs
Field-installable connectors allow on-site customization, reducing downtime during repairs or system upgrades.
5. Industry-Specific Applications
5.1 Automotive Manufacturing
Challenge: EMI from welding robots and high-vibration assembly lines.
Solution: Shielded M12 connectors with gold-plated contacts and IP69K-rated housings.
5.2 Medical Imaging
Challenge: Sterilization compatibility and signal precision in MRI machines.
Solution: Non-magnetic titanium connectors and biocompatible housings.
5.3 Agriculture and Drones
Challenge: Dust, moisture, and mechanical stress in outdoor environments.
Solution: Sealed circular connectors with ruggedized overmolds.
6. Testing and Standards
To ensure reliability, connectors must comply with:
IEC 61076: Standards for industrial connector performance.
MIL-STD-1344: Military-grade testing for shock, vibration, and corrosion.
ISO 20653: IP rating validation for environmental protection.
Testing protocols include insertion cycle tests, salt spray tests, and signal integrity analysis via eye diagrams.
7. Future Trends
Miniaturization: Nano-connectors for micro-cameras in wearable devices.
Wireless Hybrid Connectors: Combining wired reliability with wireless flexibility.
Sustainable Materials: Recyclable plastics and lead-free coatings to meet ESG goals.