Waterproofing Techniques for Outdoor Machine Vision Cables
In industrial environments, machine vision systems are often exposed to relentless vibrations from motors, conveyors, and robotic arms. While these vibrations are unavoidable, their cumulative effect on cables can lead to premature failures, signal disruptions, and costly downtime. Understanding how vibration impacts cable longevity—and how to mitigate it—is critical for maintaining reliable vision systems in industries like automotive manufacturing, food processing, and aerospace.
How Vibration Damages Machine Vision Cables
Vibration subjects cables to repetitive mechanical stress, accelerating wear through three primary mechanisms:
1. Conductor Fatigue
Microscopic Fractures: Constant bending or twisting breaks individual copper strands, increasing electrical resistance and causing signal loss.
Intermittent Connectivity: Broken conductors create flickering connections, leading to sporadic camera dropouts.
2. Connector Degradation
Fretting Corrosion: Small movements at connector pins (e.g., M12, BNC) wear away protective coatings, leading to oxidation and poor conductivity.
Loose Terminations: Vibration loosens screw-type connectors, compromising grounding and signal integrity.
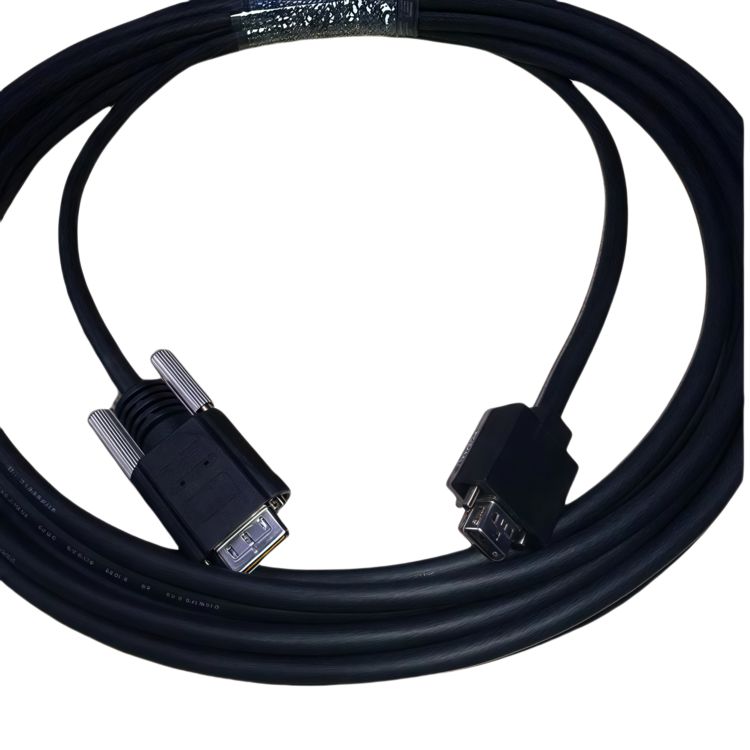
3. Jacket and Shielding Wear
Abrasion: Cables rubbing against machinery or each other develop cracks, exposing conductors to moisture and debris.
Shield Breakdown: Braided shields fray over time, reducing EMI protection and inviting noise into sensitive vision signals.
High-Risk Environments and Applications
Robotic Arms: Cables in articulated robots endure multidirectional stress during rapid movements.
Conveyor Systems: High-speed lines with vibrating sorting mechanisms.
Heavy Machinery: CNC machines, stamping presses, or hydraulic systems.
Mobile Equipment: AGVs (Automated Guided Vehicles) or drones with onboard vision systems.
Key Factors Influencing Vibration Impact
1. Frequency and Amplitude
Low-Frequency Vibration (e.g., 5–50 Hz): Causes large-scale movement, stressing cable anchors and connectors.
High-Frequency Vibration (e.g., 1–10 kHz): Induces rapid oscillations, accelerating conductor fatigue.
2. Cable Design and Materials
Stranded vs. Solid Conductors: Stranded copper handles flexing better than rigid solid-core wires.
Jacket Material: Polyurethane (PUR) resists abrasion better than PVC. Silicone jackets excel in extreme temperatures.
3. Installation Practices
Poor strain relief, over-tightened ties, or sharp bends amplify vibration damage.
Strategies to Combat Vibration-Induced Failures
1. Choose Vibration-Resistant Cables
High-Flex Cables: Designed with finely stranded conductors and durable jackets (e.g., PUR or TPE).
Look for “continuous flex” ratings (e.g., 5+ million flex cycles).
Shielded Cables: Double-layer shields (foil + braid) maintain EMI protection even as outer layers degrade.
Connector Locking Mechanisms: Screw-lock or push-pull connectors (e.g., M12 D-coded) resist loosening.
2. Optimize Strain Relief and Routing
Strain Relief Clamps: Anchor cables within 10 cm (4 inches) of connectors to absorb movement.
Use rubber-lined clamps to avoid crushing cables.
Cable Carriers (Drag Chains): Guide and protect cables in dynamic applications (e.g., robotic arms).
Ensure carriers are sized to 60–70% capacity to prevent overcrowding.
Service Loops: Leave slack in cable runs to redistribute stress points.
3. Dampen Vibrations at the Source
Anti-Vibration Mounts: Isolate cables from vibrating machinery using rubber or silicone isolators.
Adhesive Cable Tracks: Secure cables to non-vibrating surfaces with high-strength industrial adhesives.
4. Implement Redundant Connections
Dual-Port Cameras: Use cameras with redundant Ethernet ports to switch connections if one fails.
Fiber Optic Backup: Deploy hybrid copper-fiber systems for critical long-distance links.
Case Studies: Solving Vibration Challenges
1. Automotive Welding Robots
Problem: Vision cables in spot-welding robots failed every 3 months due to 20 Hz vibrations.
Solution: Replaced standard cables with continuous-flex, PUR-jacketed cables and added spring-loaded strain relief.
Result: Lifespan extended to 18 months, reducing replacement costs by 60%.
2. Packaging Machinery
Problem: High-frequency vibrations from blister-pack sealing caused intermittent camera errors.
Solution: Installed shielded drag chains and upgraded to M12 screw-lock connectors.
Result: Signal errors dropped by 90%, ensuring consistent inspection accuracy.
3. Aerospace Component Testing
Problem: Vibration testing rigs damaged coaxial cables used for high-speed imaging.
Solution: Switched to armored coaxial cables with stainless steel braiding and added vibration-damping mounts.
Result: Eliminated unplanned downtime during critical certification tests.
Maintenance Best Practices
Monthly Inspections:
Check for cracked jackets, loose connectors, or exposed shielding.
Use thermal cameras to spot hotspots caused by resistance from broken conductors.
Annual Stress Testing:
Measure signal integrity after simulating operational vibrations.
Cleaning:
Remove dust and debris from connectors using compressed air or isopropyl alcohol.