Which Materials Are Best Suited for Extremely Humid Environments
Humidity, condensation, and water immersion are among the most relentless challenges for materials in industries ranging from marine engineering to tropical agriculture. In extreme moisture-rich environments, conventional materials like untreated metals or standard polymers quickly degrade, leading to structural failures, electrical hazards, or microbial contamination.
1. The Impact of Humidity on Material Performance
Prolonged exposure to humidity can cause:
Corrosion: Oxidation of metals (e.g., rust in steel, pitting in aluminum).
Hydrolysis: Breakdown of polymers (e.g., PVC becomes brittle).
Mold and Biofilm Growth: Organic materials like wood or certain plastics foster microbial colonies.
Swelling: Absorption of water by composites, altering dimensions and mechanical properties.
Example: A Southeast Asian data center reported server failures due to copper corrosion in 95% humidity; switching to silver-plated connectors resolved the issue.
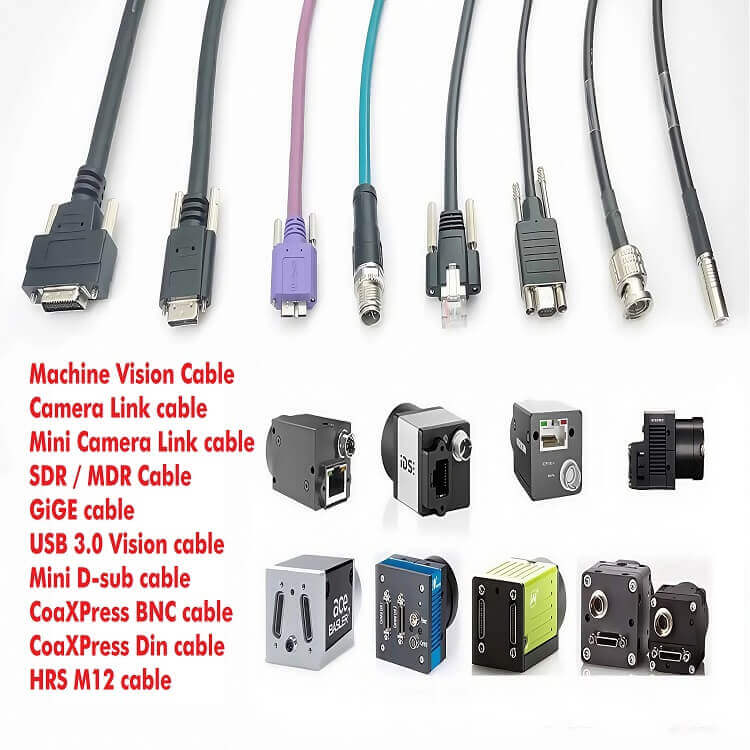
2. Key Properties for Humidity-Resistant Materials
An ideal material for humid environments should exhibit:
Low Water Absorption: <0.1% weight gain after immersion (per ASTM D570).
Hydrolysis Resistance: Stable molecular structure in water.
Corrosion Inhibition: Built-in protection against oxidation.
Antimicrobial Properties: Resistance to fungi, algae, and bacteria.
3. Top Materials for Extreme Humidity
A. Polymers and Plastics
PTFE (Polytetrafluoroethylene)
Pros: Near-zero water absorption, chemical inertness.
Cons: Poor abrasion resistance, high cost.
Applications: Gaskets in desalination plants, high-humidity lab equipment.
PPSU (Polyphenylsulfone)
Pros: Hydrolysis-resistant at 100°C/212°F, sterilizable.
Cons: Brittle below -50°C/-58°F.
Applications: Medical devices in steam autoclaves, marine sensors.
Polyurethane (PUR)
Pros: Flexible even when wet, IP68-rated formulations available.
Cons: Degrades in prolonged UV exposure.
Applications: Submersible cables, waterproof seals.
B. Metals and Alloys
Stainless Steel 316L
Pros: Resists saltwater corrosion (Mo content blocks pitting).
Cons: Heavy, expensive.
Applications: Offshore oil rigs, coastal infrastructure.
Titanium Alloys
Pros: Immune to chloride-induced corrosion, biocompatible.
Cons: Difficult to machine.
Applications: Marine implants, deep-sea submersibles.
Aluminum with Ceramic Coating
Pros: Lightweight, hydrophobic surface.
Cons: Coating can wear off.
Applications: HVAC components in humid climates.
C. Composites
Carbon Fiber-Reinforced Polymers (CFRP)
Pros: High strength-to-weight ratio, low moisture uptake.
Cons: Delamination risk if resin matrix absorbs water.
Applications: Boat hulls, drones for tropical surveys.
Fiberglass-Epoxy
Pros: Affordable, resists fungal growth.
Cons: Prone to microcracking in thermal cycles.
Applications: Water tanks, greenhouses.
D. Ceramics
Alumina (Al₂O₃)
Pros: Zero water absorption, extreme hardness.
Cons: Brittle, difficult to shape.
Applications: Insulators in high-voltage marine equipment.
Silicon Carbide (SiC)
Pros: Thermal shock resistance, impervious to moisture.
Cons: High manufacturing cost.
Applications: Pump seals in chemical processing.
4. Protective Coatings and Treatments
Graphene Coatings: Ultra-thin, hydrophobic layers that block moisture penetration.
Zinc-Nickel Plating: Sacrificial corrosion protection for steel fasteners in humid air.
Silicone Impregnation: Waterproofs porous materials like concrete or textiles.
Case Study: Singapore’s Marina Bay Sands uses graphene-coated steel in its rooftop infinity pool infrastructure to combat 85% annual humidity.
5. Industry-Specific Solutions
Marine Engineering
Material: Hybrinet® (PTFE-coated stainless steel mesh).
Use: Anti-biofouling nets for aquaculture.
Electronics
Material: Liquid Crystal Polymer (LCP) films.
Use: Moisture-resistant flexible circuits in wearable devices.
Construction
Material: ACC (Autoclaved Aerated Concrete) with silicone additives.
Use: Mold-resistant walls in tropical housing.
6. Testing Standards for Humidity Resistance
ASTM D5229: Measures water absorption in composites.
ISO 9227: Salt spray testing for corrosion resistance.
IEC 60068-2-78: Evaluates material stability in 93% humidity at 40°C.
Pro Tip: For critical applications, conduct cyclic humidity tests (e.g., 24h at 95% RH, 24h drying) for 30+ cycles.
7. Cost vs. Performance Analysis
Material Cost Index (PVC=1) Lifespan in Humidity
PVC 1.0 2–5 years
PUR 2.5 10+ years
Stainless Steel 316L 6.0 30+ years
PTFE 8.0 50+ years
ROI Example: A Florida resort replaced wooden decking with recycled HDPE (0% water absorption), saving $200K in maintenance over 10 years.
8. Future Innovations
Self-Healing Polymers: Repair microcracks caused by humidity cycles.
Bio-Inspired Surfaces: Lotus-leaf-effect textures for superhydrophobic metals.
Moisture-Harvesting Composites: Materials that extract drinking water from humid air.