Why Custom-Made Machine Vision Cables Are Worth the Investment
- Optimized Performance for Complex Systems
Generic cables are designed for broad compatibility, but they lack the precision required for advanced applications:
Signal Integrity: Custom cables are impedance-matched (e.g., 75 Ω for CoaXPress, 100 Ω for Camera Link) to minimize reflections and signal loss. This is critical for high-resolution cameras (e.g., 25 MP+) operating at 60+ fps.
Bandwidth Customization: Tailored conductor sizes (e.g., 28 AWG for short runs, 22 AWG for long distances) ensure minimal attenuation (<0.5 dB/m at 10 GHz). EMI/RFI Shielding: Custom shielding configurations—such as dual-layer foil and braid—achieve >90 dB noise suppression in environments with motors, VFDs, or wireless devices.
Case Study: A semiconductor manufacturer reduced image noise by 70% by upgrading to custom cables with double-shielded coaxial lines and ferrite cores near connectors.
2. Enhanced Durability in Harsh Environments
Industrial settings demand cables that withstand extreme conditions. Custom solutions address these challenges head-on:
Material Selection:
High-Temperature: Silicone jackets (up to 200°C) for foundries or near ovens.
Chemical Resistance: FEP or TPE jackets for washdown areas (IP69K) or exposure to oils/solvents.
Abrasion Resistance: Reinforced aramid yarns for cables routed through robotic arms or cable chains.
Mechanical Resilience:
Bend Radius: High-flex designs with a bend radius as low as 3× cable diameter for continuous motion (e.g., 10 million flex cycles in pick-and-place robots).
Strain Relief: Overmolded connectors with IP67/68 ratings prevent wire breakage in vibrating machinery.
Example: A food packaging line using custom PUR-jacketed cables with stainless steel connectors saw a 50% reduction in cable replacements despite daily high-pressure washdowns.
3. Reduced Downtime and Maintenance Costs
Off-the-shelf cables often fail prematurely due to mismatched specifications, leading to unplanned downtime. Custom cables mitigate this risk:
Longer Lifespan: Industrial-grade materials and construction extend service life by 3–5× compared to standard cables.
Predictable Maintenance: Custom cables are tested for flex life (e.g., 10 million cycles per IEC 61076) and include traceable documentation for proactive replacement scheduling.
Plug-and-Play Compatibility: Tailored lengths and connectors eliminate field modifications, reducing installation errors.
ROI Calculation: A
500
5
500customcablelasting5yearscosts100/year, while a
200
200genericcablereplacedannuallycosts200/year—a 50% savings over time.
4. Seamless Integration with Existing Infrastructure
Custom cables bridge compatibility gaps in multi-vendor systems:
Hybrid Connectors: Combine multiple protocols (e.g., GigE Vision + 24V power) in a single cable to simplify wiring.
Length Precision: Avoid signal loss from excess cable coiled in control cabinets.
Color Coding and Labeling: Customized markings streamline troubleshooting and maintenance.
Application: A logistics company integrated vision-guided robots using custom 15-meter cables with hybrid M12 connectors (data + power), cutting installation time by 40%.
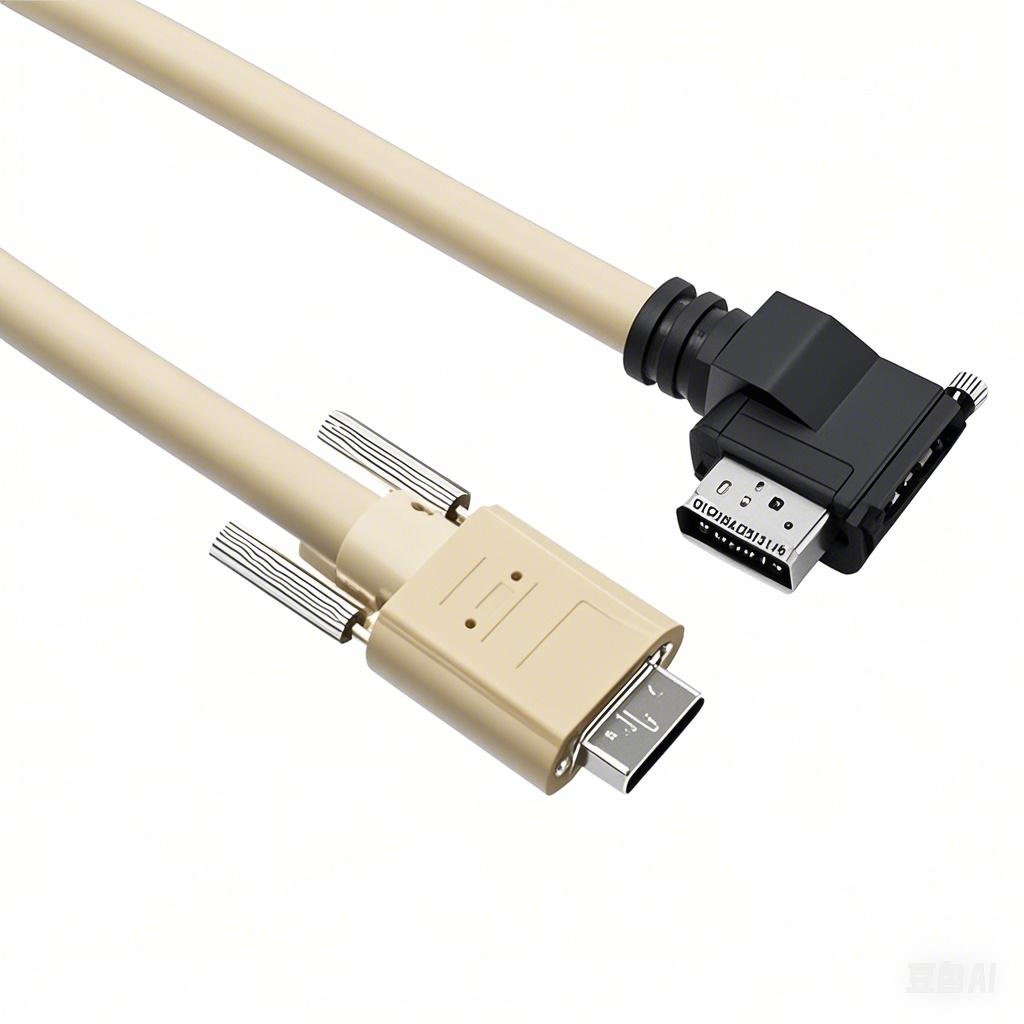
5. Compliance with Industry Standards
Custom cables ensure adherence to stringent regulatory and safety requirements:
Certifications: UL, CE, RoHS, and FDA-compliant materials for industries like pharmaceuticals or automotive.
Flame Retardancy: LSZH (Low Smoke Zero Halogen) jackets for use in confined spaces or public infrastructure.
ESD Protection: Static-dissipative materials for cleanroom environments.
6. The Custom Cable Design Process: What to Expect
Requirement Analysis:
Define signal types (e.g., CoaXPress, USB3 Vision), bandwidth, environmental conditions, and bend cycles.
Prototyping:
Test samples for signal integrity (TDR testing), flex endurance, and EMI performance.
Certification and Documentation:
Obtain test reports and compliance certificates tailored to your industry.
Partner Tip: Work with manufacturers offering 24/7 engineering support and rapid prototyping (2–4 weeks).
Cost vs. Benefit: Breaking the “Expensive” Myth
While custom cables have higher upfront costs (typically 20–50% more than generic options), their long-term benefits dominate:
Factor Generic Cable Custom Cable
Lifespan 6–12 months 3–5 years
Downtime Cost
10
–
10k–50k/hour in production loss Near-zero with predictive maintenance
Replacement Labor 2–4 hours per incident Eliminated